Safety Testing
Electrical safety testing of arc welding equipment should be carried out periodically (normally annually), during servicing, before Calibration to EN IEC 60974-14 & after repair of equipment. Engineers use different methods for ‘safety testing’ of welding equipment including PAT tests & Megger tests. However, unless you are using specialist equipment for testing arc welding power sources your testing will not comply with this standard. PAT testeing and Megger testing alone are insufficient to guarantee safety.
The welding power source can be tested with any ancillary equipment fitted that can affect the test results i.e. water coolers etc. This standard is not applicable to the testing of new power sources or engine-driven power sources.
The MCT Unit (Machine Compliance Test Unit) when used in conjunction with the documentation software ensures compliance with IEC 60974-4. The standard has been introduced to ensure the electrical safety of welding equipment, which in turn will protect the machine user or persons tasked with repairing and calibrating the equipment from serious injury or worse.
This part of IEC 60974 specifies test procedures for periodic inspection, and after repair, to ensure electrical safety. These test procedures are also applicable for maintenance. This standard is applicable to power sources for arc welding and allied processes designed in accordance with IEC 60974-1 or IEC 60974-6. Stand-alone ancillary equipment designed in accordance with other parts of IEC 60974 may be tested in accordance with relevant requirements of this part of IEC 60974.
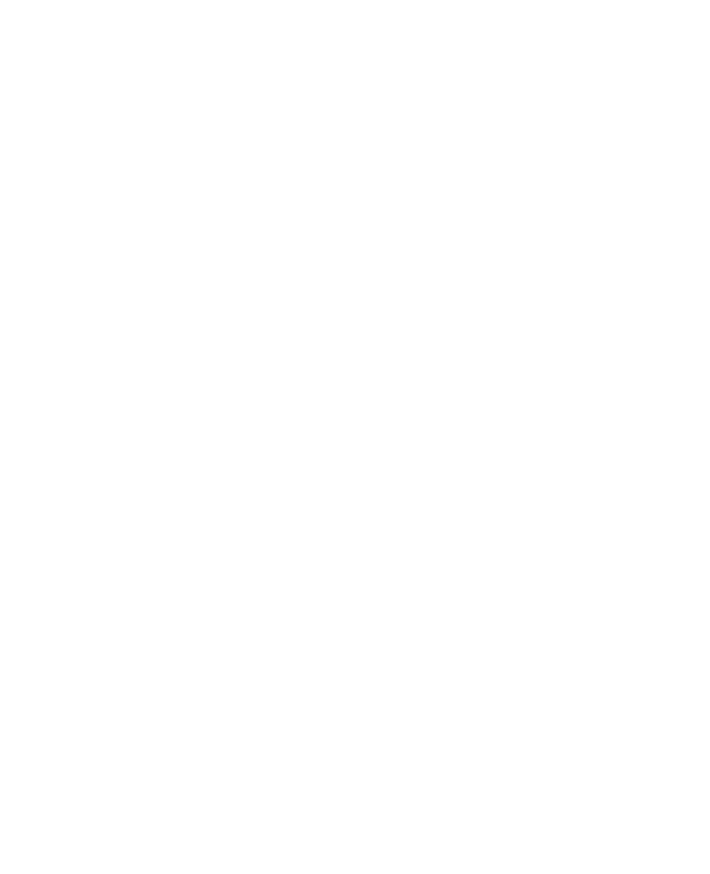
Test Procedures
During the procedure we will carry out a detailed Visual inspection and test the earth circuit of the primary supply to make sure it is present and connected correctly. We will also test (using a generated 500v) for leakage, from the Primary supply to earth, the secondary supply to earth and for any leakage between the primary and secondary circuits.
When testing a machine after a repair, we will carry out a function = test to the welder. The owner of the equipment has the responsibility of the safety level and that the inspection has been made in time. Tests of welding equipment can be hazardous and shall be carried out by a trained and certified expert in the field of electrical test and repair, who is familiar with welding, cutting and allied processes.
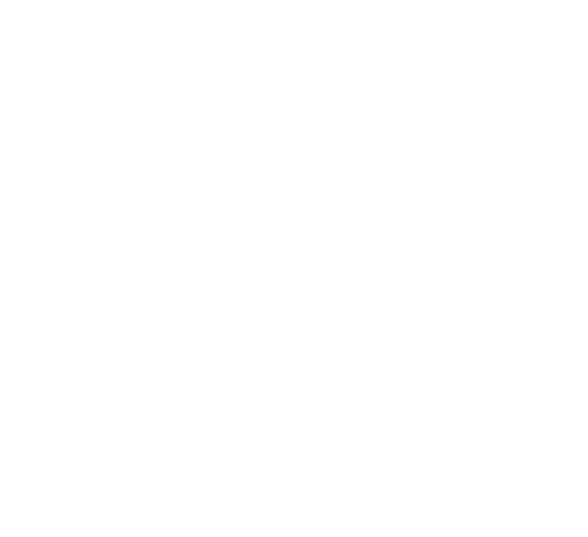
Only expert test personnel can open the equipment. This procedure must be carried out after any repair to a part or replacement of a part that restores a welding of cutting function. For example changing a wheel will not affect a welding or cutting function therefore does not restore it, in this case a test is not required. If, for example, a PCB is replaced or repaired, a welding socket is replaced or ANY other component affecting welding or cutting, then the test must be carried out.
Different manufacturers specify the intervals at which their equipment must be tested. Most are 12 months but a list of manufactures and their recommendations are at the back of this document. If the manufacturer is not on the list, then contact must be made with the manufacturer to determine how often the test must be done. Please note that the conditions in which the machine operates
can affect the interval (eg. machines used off shore and in ship yards are typically tested every 6 months).
It is recommended in IEC 60974-14, the standard for Calibration and Validation of Arc Welding Equipment, that the procedure is carried out prior to Calibration or Validation.